Have you watched the recent Chinese blockbuster film, The Wandering Earth 2? If you haven’t, spoiler alert.
The movie brings a classic sci-fi trope to life: exoskeletons.
While The Wandering Earth 2 is primarily a figment of the director’s imagination, its portrayal of exoskeletons is close to reality. In fact, here’s a little trivia: due to the heavy load of outdoor set props, the production team opted to transport them using exoskeletons developed by Chinese robotics company ULS Robotics.
Active and passive exoskeletons, explained
In real life, exoskeletons are donned for the same reason as the characters in the movie: mobility support and assistance. They are therefore highly applicable to the context of healthcare. For example, patients with hemiplegia or limited mobility can be fitted with exoskeletons to manage their range of motion, which could improve the efficacy of physical rehabilitation.
Exoskeletons used in this context are generally known as passive exoskeletons. These robotic wearables can be fitted to support and train patients’ physical activity while they undergo physical rehabilitation. Medical exoskeletons do not usually require power to operate and are designed with a bias towards constraint. By restraining the physical movement of patients at various points of their body, such as their knee joints, they help simulate natural gait, potentially improving rehabilitation results.
Their weight reduction and shock absorbing qualities may also aid patients in better managing the rigorousness of physiotherapy sessions, particularly those with significant physical immobility.
Medical exoskeletons were the initial focus of Zhenhua Xu, founder of ULS Robotics, when he first started to develop the technology. However, Xu found it difficult to overcome extrinsic limitations of the technology: high costs and the lack of alternative use cases. At that time, exoskeletons were mainly used in hospitals, and were unaffordable for the average individual as each unit cost upwards of thousands of dollars.
Besides its medical applications, exoskeleton technology finds relevance in both military and industrial sectors. Factories, in particular, tend to be more open to the promotion and implementation of the technology, creating a more favorable environment for the growth of the technology.
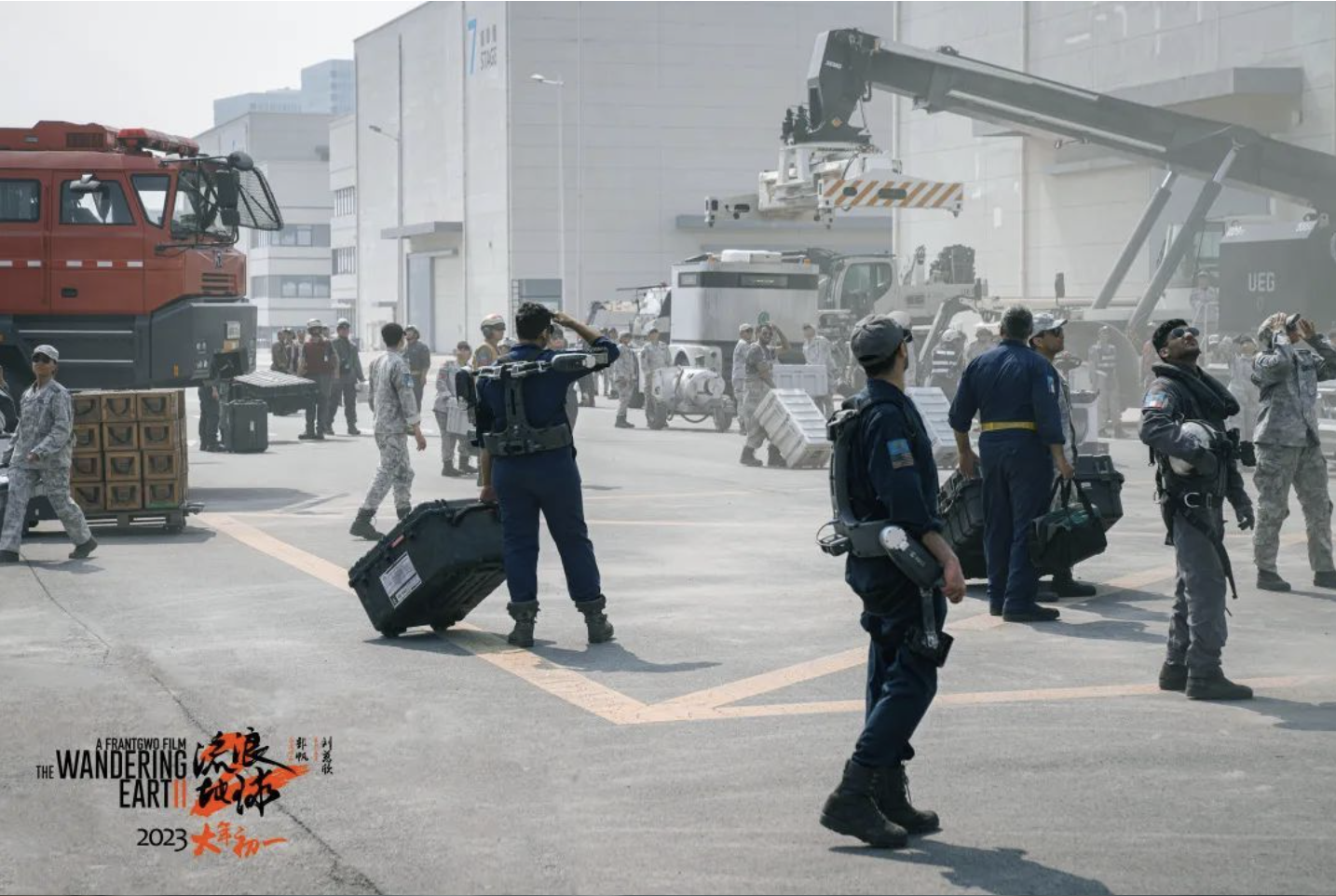
Exoskeletons used for industrial activities may resemble what is conventionally regarded as “sci-fi armor.” They fall under the category of active exoskeletons and are typically powered to enhance physical strength and endurance while retaining a flexible range of motion. Such exoskeletons are therefore useful when utilized to perform labor-intensive tasks such as construction and mining, particularly in non-deterministic scenarios.
Current exoskeletons deployed in industrial settings can be further categorized into two types: full-body and modular. Modular exoskeletons focus only on certain body parts, such as the waist or limbs. They can also be subcategorized based on the amount of assistance provided and are typically expressed in kilogram units, based on the weight reduction benefits:
- R1: 5–15 kilograms
- R2: 15–30 kilograms
- R3: 30–50 kilograms
- R4: Over 50 kilograms
Other exoskeleton variations exist. For example, modular exoskeletons have been used to provide lumbar support for workers, potentially reducing the occurrence of spine-related occupational diseases.
According to Xu, ULS Robotics’ exoskeleton products have been designed to fit the needs of various sectors including logistics, home appliance manufacturing, aviation logistics, power generation systems, and more. Its exoskeletons are donned by coal miners, pipelayers, transporters, among others. For the average laborer who carries a load between 30–50 kilograms and bends over more than 1,000 times a day, exoskeletons can offer physical support that is potentially life changing.
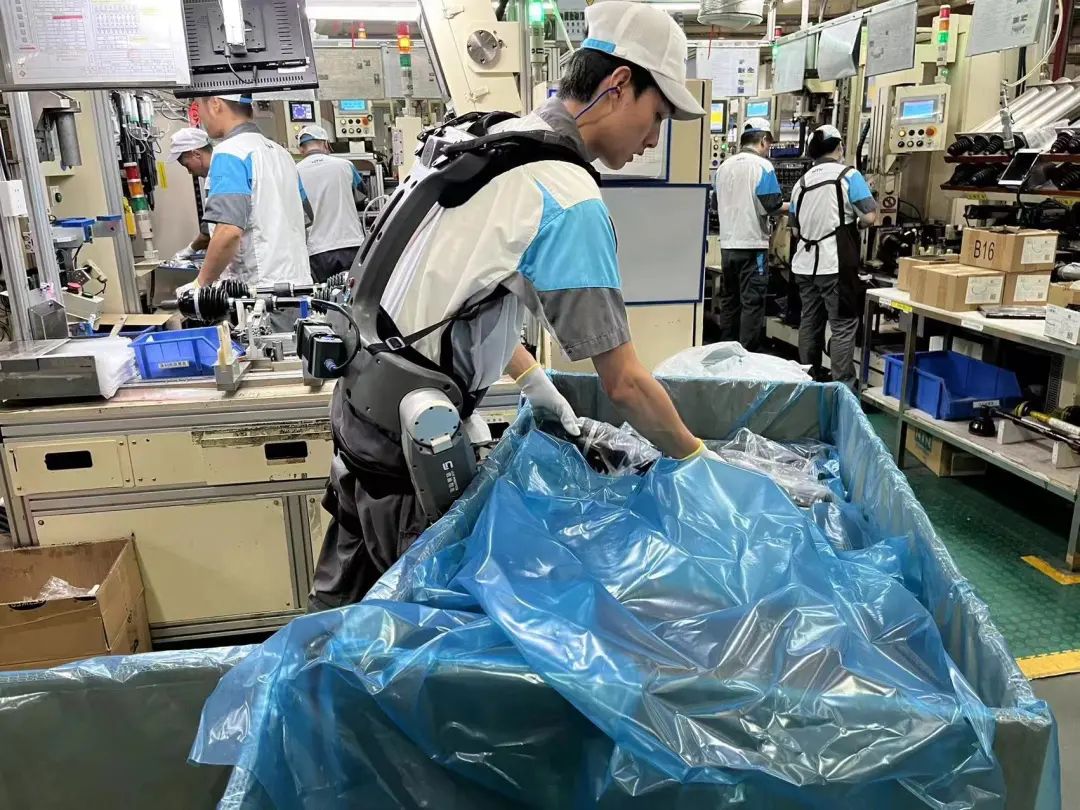
Path toward mainstream adoption
While ULS Robotics has obtained CE certification in Europe, indicating that its products meet the European Union’s safety and quality standards, a long road lies ahead for the exoskeleton market that remains underdeveloped in several areas including software, hardware, and other aspects like raw materials.
In the interim, ULS Robotics has continuously iterated its exoskeleton products to optimize three key aspects: cost, stability, and compactness. In 2019, its first-generation waist exoskeleton weighed 10 kilograms and could bear a maximum load of 20 kilograms. The latest version now weighs 5.8 kilograms and can bear 50% more weight (30 kilograms) than the original version.
The Chinese robotics company has also created an internet-of-things platform capable of managing exoskeletons while collecting data in real time. The platform offers a customizable user experience, enabling them to adjust its settings to fit a variety of use cases. For example, users can adjust the amount of weight support provided by an exoskeleton at each body part, such as the hip, arms, and legs. The software enables movement and environment tracking as well, facilitating analyses of movement intent.
ULS Robotics is not alone in the field of exoskeleton development. Ottobock, a German orthopedic technology company, and Japan’s Innophys, are examples of other exoskeleton technology developers. Multinational conglomerates such as Samsung and Honda are also exploring the use of exoskeletons to provide physical and mobility support to the elderly.
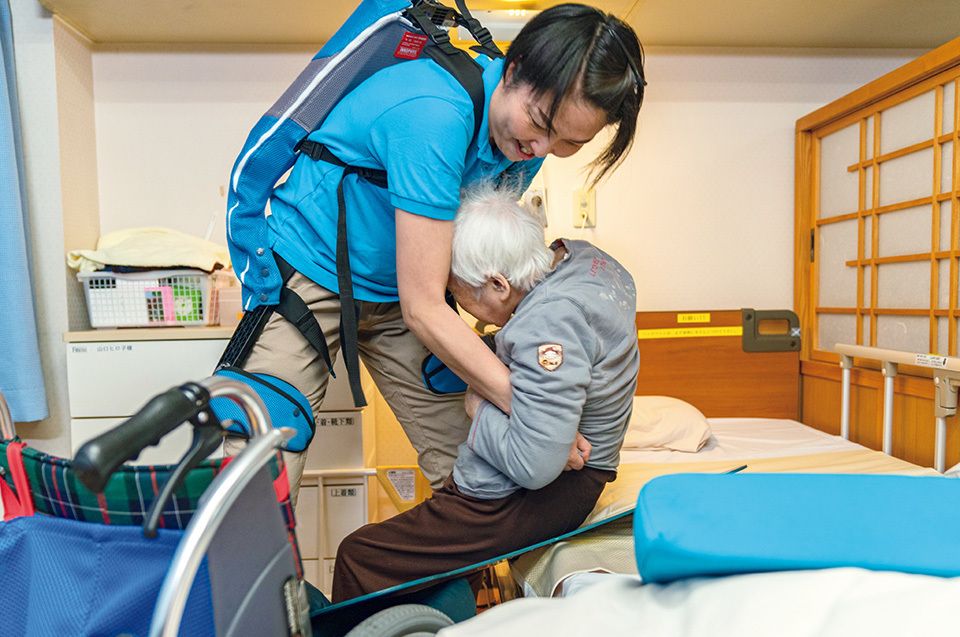
Still in its early stages of development, the tipping point for exoskeleton technology to go mainstream will likely depend on its adoption rate among the general population in the near future, according to Xu.
In industry settings, exoskeletons may complement unmanned or autonomous robotics, enhancing human-robot interactions while predicting and adapting to user behavior patterns. They can also be utilized by workers who are required to adapt swiftly to changes in their environment, particularly those who work in the manufacturing, logistics, and chemicals industries. Exoskeletons can improve their efficiency while reducing the risk of experiencing occupational hazards.
Furthermore, in countries with an aging workforce, such as Japan, South Korea, and parts of Europe and the US, labor protection laws and a growing emphasis on health and safety presents opportunities to spur demand for exoskeleton products.
Nonetheless, the timeline for achieving maturity in exoskeleton technology varies from company to company, contingent upon both hardware and software considerations.
For hardware, specialized companies might possess distinct advantages in terms of engineering details and designs. For example, Ottobock’s profound grasp of human anatomy gives it a competitive edge in the development of exoskeleton mechanics.
The key issue that remains for most companies in this field is their lack of chip production capabilities.
Specific to ULS Robotics, its expertise lies in software, having independently developed its core exoskeleton technology while registering over 40 patents and software copyrights in the span of a few years. Its endeavors have not gone unnoticed, as the company recently completed its Series A round, poised to finance the development of new products and its marketing efforts.
KrASIA Connection features translated and adapted content that was originally published by 36Kr. This article was written by 36Kr.